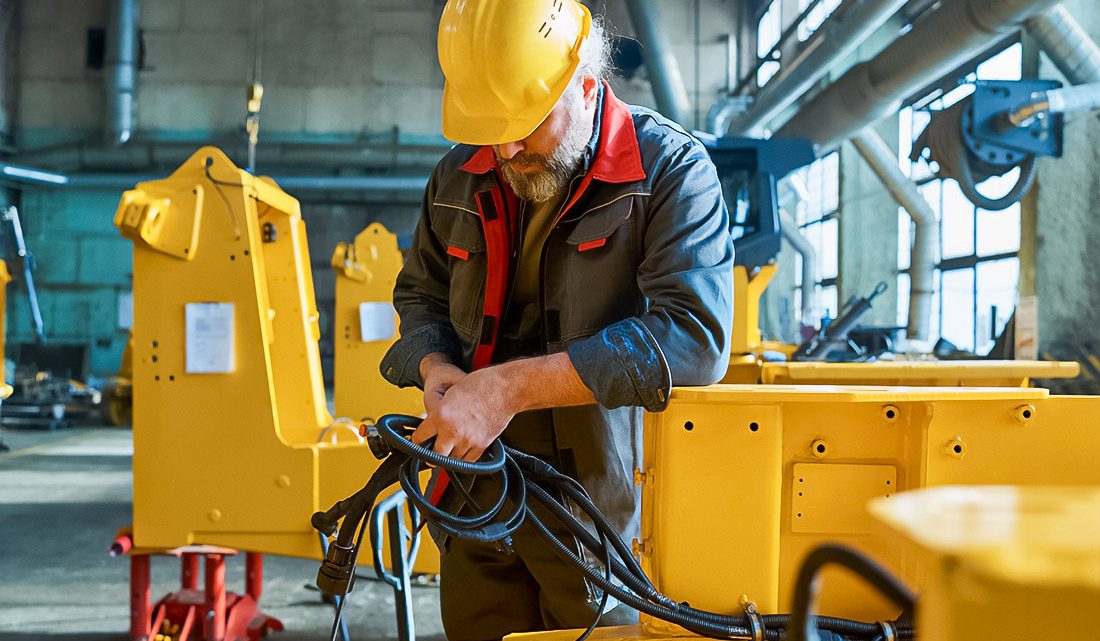
Revolutionary Solutions in the Field of Seals for Multistage Pumps: Mechanical vs. Magnetic
Technological Breakthroughs in Sealing Systems
Multistage pumps, finding application in chemical, oil, and other industries, are presented as highly efficient devices. However, their reliability largely depends on the quality of the seals. Only in the UAE is the annual seal market estimated at 14 billion AED. In 2023, there was a growth of 5%, emphasizing their importance in industrial systems. Learn more about multistage pump repair and their maintenance.
Evolution and Role of Mechanical and Magnetic Seals
- Mechanical Seals: Such a system is represented by a complex structure of various elements. Their integration into the pump ensures exceptional tightness, allowing the use of pumps at pressures up to 200 bar and temperatures up to 300°C. Examples of successful use include BASF chemical plants and Shell refineries.
- Magnetic Seals: Technology of contactless sealing, providing low wear. It began to be used in 1980 at jet fuel production plants. They are successful in environments with strong acidity and temperatures above 500°C.
Analysis of Causes and Consequences of Mechanical Failures
Mechanical systems often fail for trivial reasons. Examples include:
- Wear of components manifests itself after 5,000 hours of operation in unmaintained pumps.
- Overheating caused failure at Chevron plants, leading to a loss of 1.2 million AED.
- Critical damage in just six months of operation.
Consequences can vary from increased decibel levels (up to 85 dB, violating industrial standards) to complete shutdowns of pumps, as was recorded in Ohio in 2019. More about mechanical seals.
Magnetic Failures: Hidden Threats
Although magnetic seals are traditionally reliable, sometimes difficulties may arise:
- Loss of properties is observed in 13% of outdated magnets.
- Displacement of rings in 80% of cases leads to leaks, requiring careful monitoring of the system.
Such cases are especially dangerous at high-purity chemical production plants, where every drop is important.
Comparison: Mechanical vs. Magnetic Seals
Obvious differences:
- Mechanical shows up to 30% more wear compared to contactless systems.
- Magnetic withstand temperatures increased by 150°C and more, making them versatile for rigid-type reactors.
- Maintenance requirements for mechanical systems are 40% higher, increasing operational costs in the long run.
Modern Approaches to Failure Diagnosis and Prevention
To prevent unwanted shutdowns, the following steps should be taken:
- Scheduled inspections every 3 months.
- Real-time monitoring conducted with AI systems delegated analysis.
- Use of 4th class durability materials, extending the resource by 25%.
- Correct installation, which eliminates problems in 90% of failure cases at the assembly stage.
How to Make a Choice in Favor of the Best Sealing Solution
The decision of which seal to use lies in the details:
- In conditions of high environmental aggressiveness — choose magnetic.
- If minimal personnel for maintenance is required — again magnetic.
- For budget savings, use mechanical.
The choice based on current industrial materials ensures up to 98% stability. Regular monitoring of system and component integrity is critically important for successful pump operation, as proven by the example of ExxonMobil, where the implementation of a comprehensive maintenance program reduced costs by 40% in just a year. Learn more about the application of modern technologies in sealing systems.
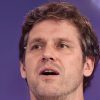
Basketball fan, Shiba Inu lover, DJ, writer and designer of various specialties. We work at the intersection of simplicity and informatics to save the world from bad design. Sometimes I do random things with friends. I am developing my own business.
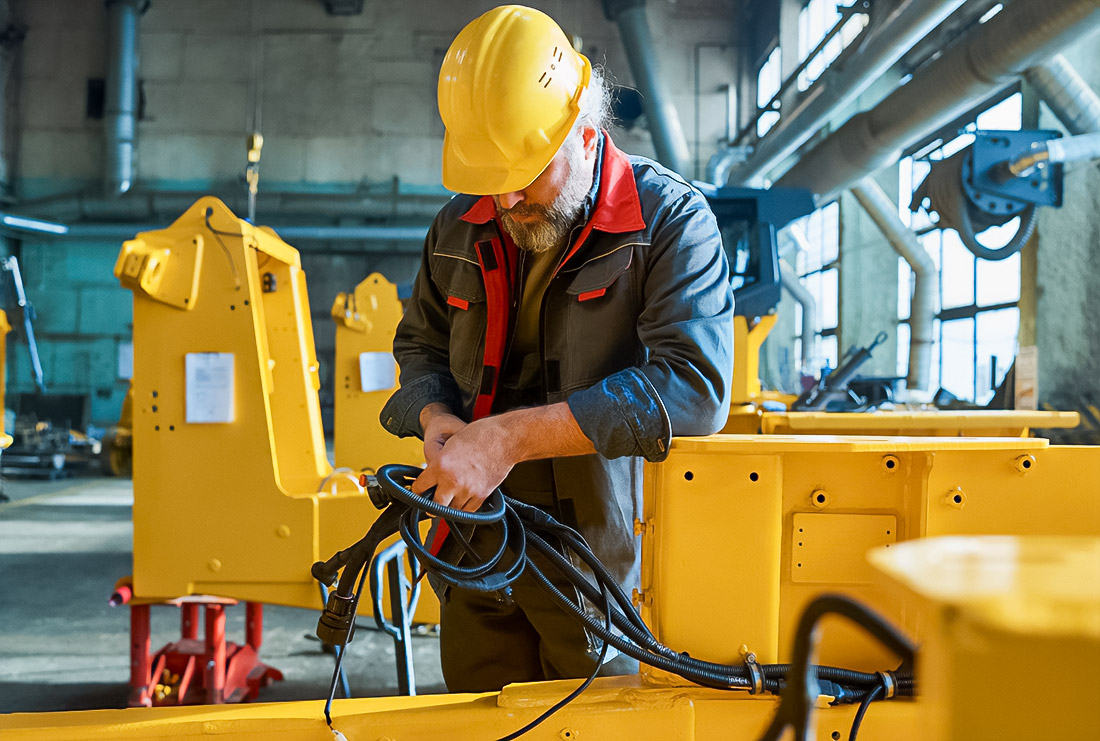